How To Maximise Productivity In Your Factory
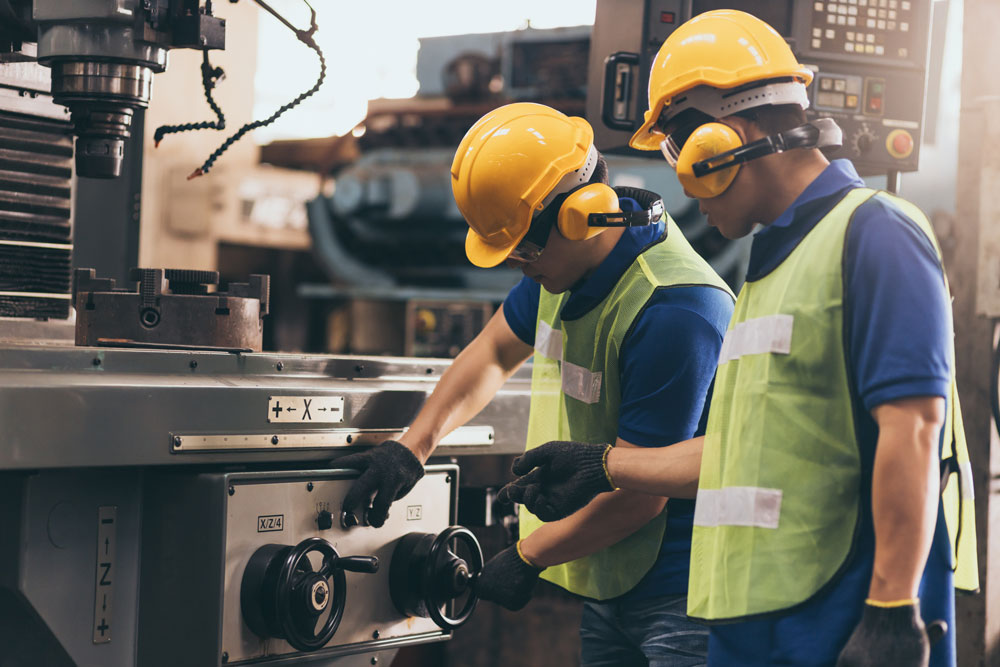
- Improve waste management
- Re-think the arrangement of your facility
- Invest in new technology
- Provide training to employees
- Enhance internal communication
The manufacturing industry was responsible for £358.7 billion in sales in 2020, according to the ONS. Given this vast amount, maximising efficiency in the workplace should be a priority for factory managers.
There are many measures you can take to increase productivity in your factory, from enhancing internal communication to providing regular training for staff.
At ICE Cleaning, we have years of experience in factory cleaning. Utilising advanced solutions and techniques, our technicians can return your factory to a safe environment. We operate 24/7, 365 days a year.
Continue reading to learn about some of the methods you can adopt to maximise productivity in your factory.
Improve waste management
Reducing the amount of waste you dispose of can help save you money. If you have left-over products that haven't been utilised, consider re-using the material for something else.
Part of waste management is effectively controlling your inventory. Take careful stock of how much material you use, and only buy as much as you produce. This will save you on over-spending and waste simultaneously.
At ICE Cleaning, our factory cleaners can help you out here. During the clean, we can carry out waste disposal if you need it. Just let our friendly support team know, and we will be able to accommodate this.
Re-think the arrangement of your facility
Re-arranging the plan of your facility can help to improve the productivity of your team, making the manufacturing process easier. Optimising the layout also means staff spend less time searching for products.
This solution may increase your output, as operations are not disrupted by a confusing floor design. It benefits staff too, as the organisation makes their jobs more straightforward.
You should take time to assess the arrangement of your facility, thinking logically about what layout will work best. Once you have done this, it is time to implement it.
Output could increase when the layout is optimised, as time spent navigating the factory is reduced. Additionally, this measure can prevent accidents from occurring. Heavy lifting won't be required as often, and slips trips and falls are less likely to take place.
Another good way of reducing accidents is to hire in a professional factory cleaning company. They will carry out a deep clean of the area, and can remove debris from the ground and treat any slippery substances.
Ensure health and safety remains a priority by taking a look at our blog about the most common causes of industrial accidents.
Invest in new technology
Adopting new technology for the workplace is another way you can maximise productivity. It enables processes to be streamlined so that work can be completed quicker.
Increased automation can save you money too, as less manual labour is needed. Emphasis should be placed on machinery that can make your individual workplace more efficient. Take a look at your operation and see what could be improved.
It is worth consulting staff members here, as they use these processes every day. They could suggest areas for investment that you hadn't thought of.
Though often a heavy investment up-front, updating equipment has many benefits. Workers will be happier when operations are improved, while you can focus on meeting your KPIs.
Provide training to employees
Although training is provided in workplaces, consistently investing in new training resources and courses can increase efficiency. You spread knowledge by offering training on different aspects of the business, meaning that if a member of staff is absent there isn't a gap in experience.
It is also important to keep this in mind as technology is always advancing. Knowing how to utilise new machinery will speed up operations and allow you to reach your target output.
Another benefit is that employee satisfaction is likely to increase if you're investing in career development. This could result in greater employee retention as employees are given the opportunity to develop their skills and knowledge.
Regular training should emphasise the importance of maintaining health and safety in the workplace. This will help to prevent accidents and minimise any downtime that would have been experienced due to any accidents.
To learn more about training your staff, have a look at this useful article provided by the Health & Safety Executive (HSE).
Enhance internal communication
Encouraging more collaboration between team members is a great way to increase productivity. Mis-communication over tasks will potentially lessen with improved dialogue, which can often cause delays and mistakes.
Internal communications could include meetings about any updates or changes to operations, or asking staff for feedback.
You gain respect from your employees when you listen to their concerns or thoughts. Morale is boosted when internal communication is prioritised, making for a happier workforce.
Enhancing communication will also help with task organisation too. For example, staff are aware of any inventory problems that could delay operations, and are less likely to miss deadlines because they are kept well-informed.
Contact our friendly team today
Reach out to us on 0208 066 0360 or enquiries@icecleaning.co.uk to find out more about the industrial and factory cleaning services we provide. We're here to help you with whatever support you require.
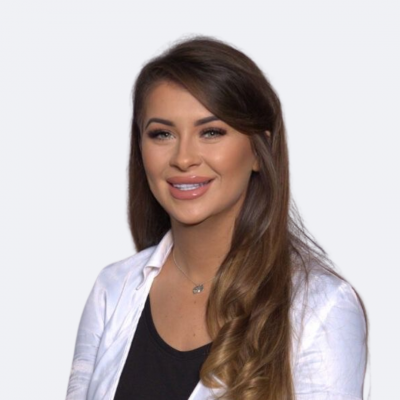
Speak with me today,
I’m here to help
By asking you a few questions either via phone or email I can immediately provide a realistic estimation of the cost.
You’re in good company. We’ve cleaned for the following commercial clients… View all
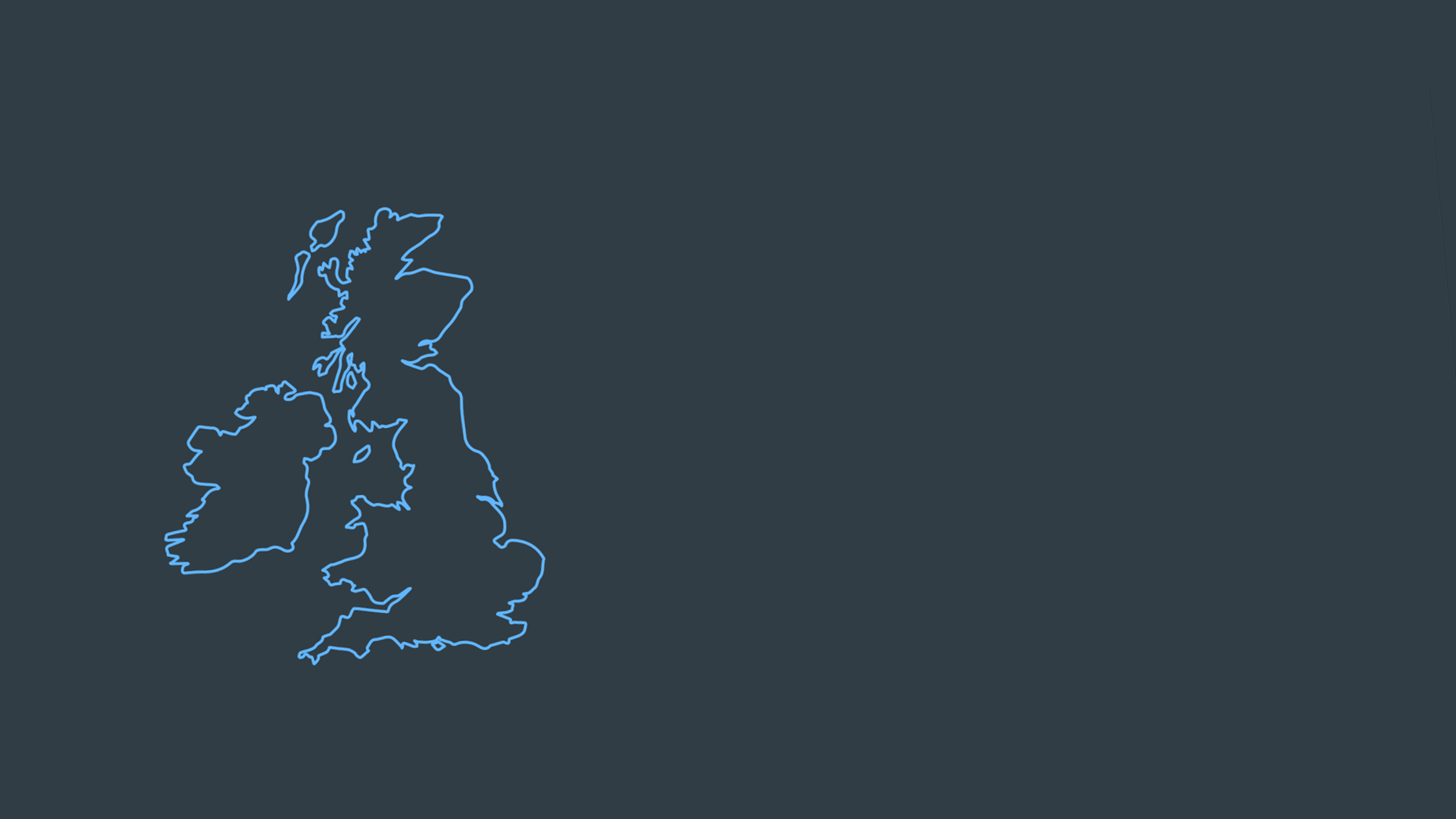
Why choose us?
- Cater to a wide variety of cleaning situations
- Nationwide coverage, available 24/7
- Cater to commercial and domestic clients
- Free survey provided prior to quotation
- Emergency response team
- Offer a bespoke service designed to suit all your needs
- All technicians hold professional health and safety qualifications, including BICSc, IOSH, Dewpoint Professional & Safe Contractor
We’re fully accredited
We place best practise, professional expertise and health and safety at the core of our business. We’re fully compliant with all legal obligations. You can view a list of our accreditations below, or visit our Health & Safety page for more information.
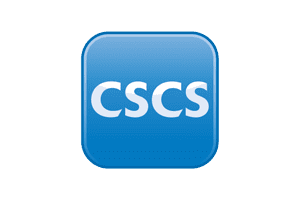
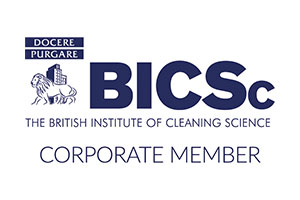
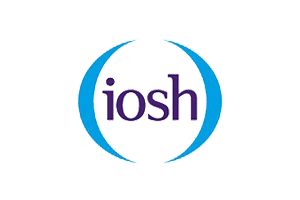
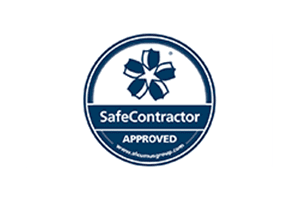
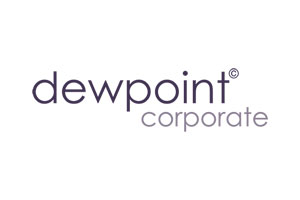
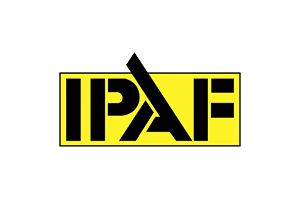
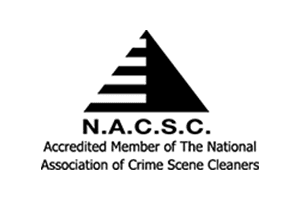