How To Reduce Inventory Costs In Your Warehouse
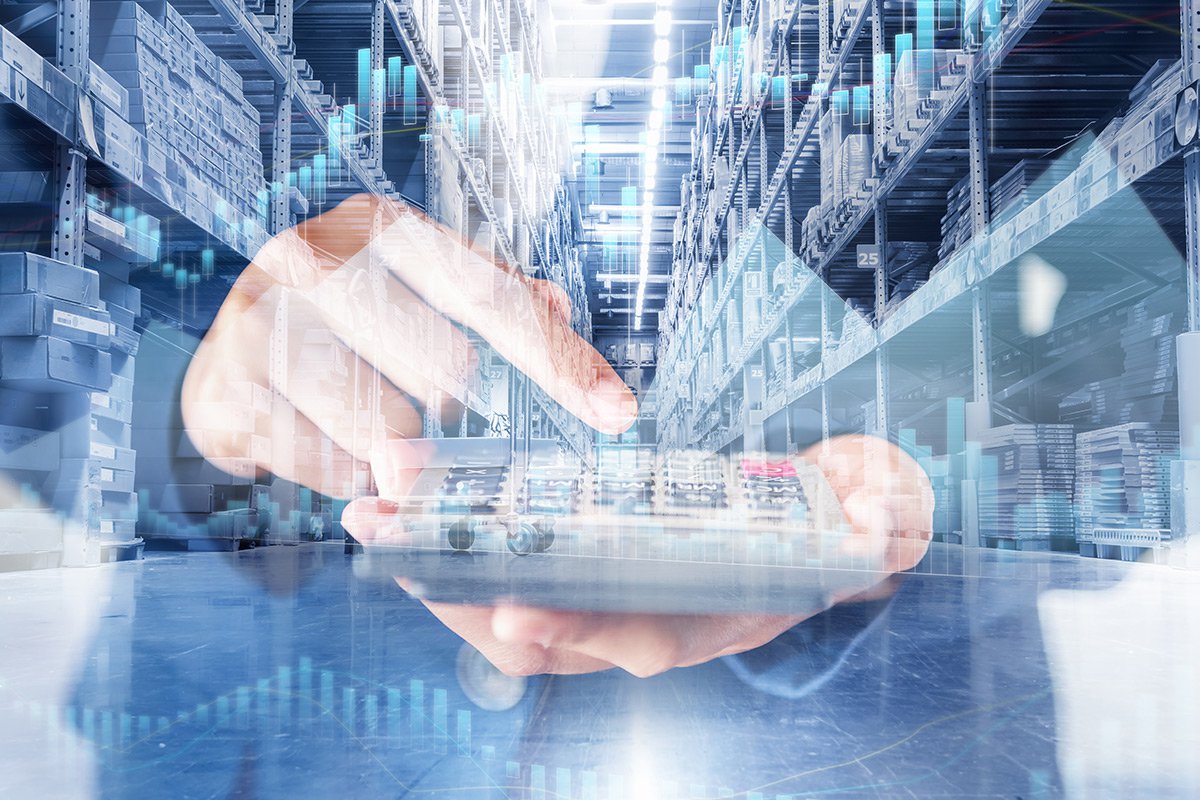
CONTENTS
- How to reduce inventory costs in your warehouse
- Improve supplier lead time
- Automate your inventory
- Manage your SKUs
- Invest in high-quality logistics software
- Dispose of obsolete inventory
- Monitor workforce performance
How to reduce inventory costs in your warehouse
Logistics companies face the challenge of operating efficiently whilst keeping costs down. Warehouse storage is expensive, so careful planning is required to remain cost-effective.
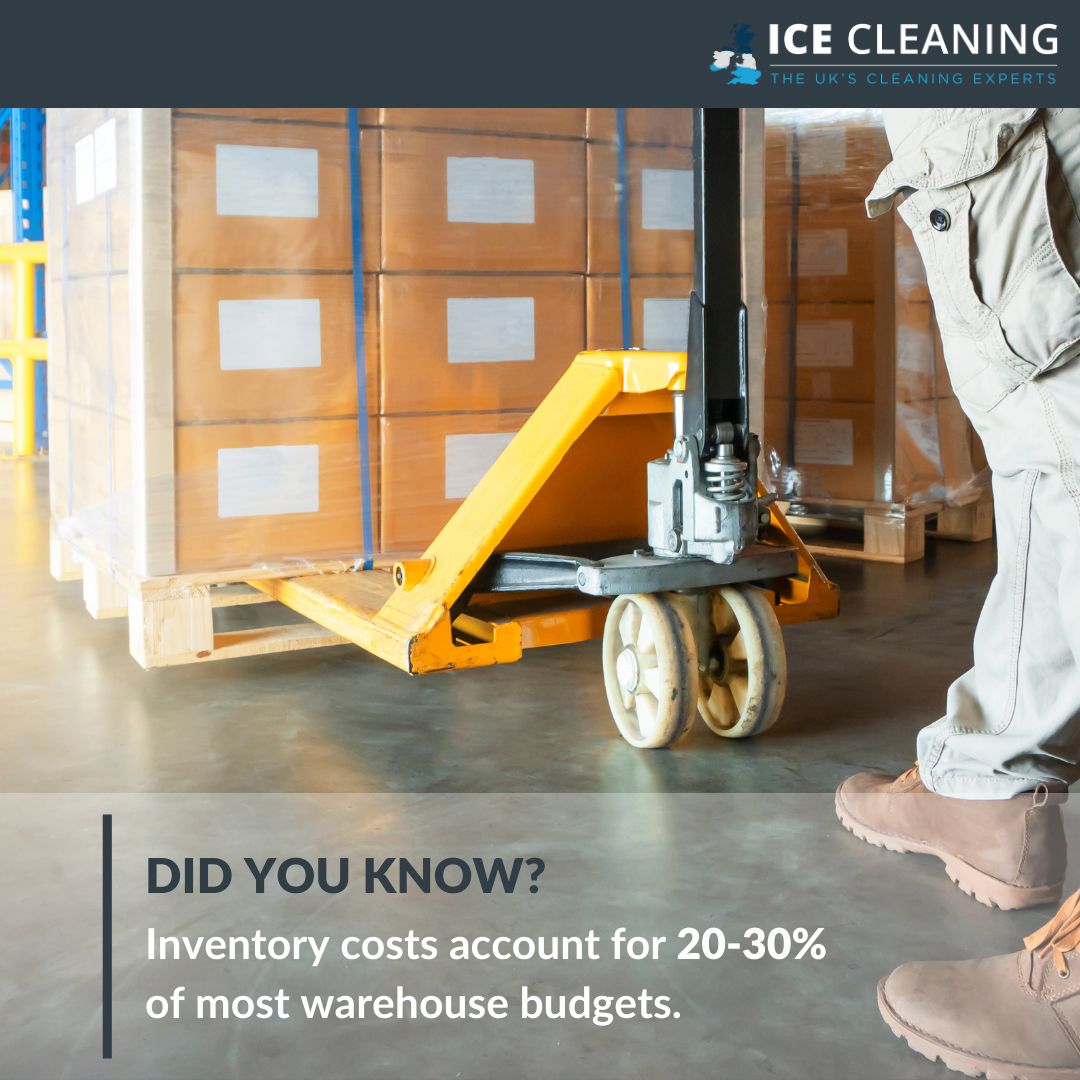
Typically, inventory costs account for around 20-30% of the budget. By reducing costs by just 5%, your business could gain a competitive advantage over comfortable rivals.
By making a few small changes, you can fully utilise your operations. Over time, you may be able to seize a higher market share and enjoy greater profits.
Improve supplier lead time
Lead time plays a huge role in inventory management. Lead time refers to the length of time between placing your order with your supplier and receiving your stock.
By reducing your lead time, you can benefit from carrying less stock. This will lower the costs involved in both transportation and storage.
Of course, buying less stock at a time will mean that you have to place orders more frequently. Though this may seem like a drawback, it can save unnecessary costs in the long run.
Whilst you may not benefit from bulk shipping costs, the pressure of minimum order quantities will be reduced. As a result, you’ll order only what you actually need, meaning no costs will be spared.
Improving your supplier lead time can be particularly profitable for companies ordering from domestic suppliers. Purely domestic supply chains will be more predictable than international suppliers, leading to more accurate forecasts.
To manage your supply chain, you may choose to automate the transmission of information.
Automate your inventory
Inventory automation has been adopted by businesses of all sizes. Technical advancements have made automation a feasible option for even small businesses, so whether you operate on a national or global scale, you can benefit from faster processes.
For growing businesses, automation aids the pressure of managing multiple departments. Expansion adds more stages of approval in your supply chain, making for a lengthier, more complex process. The right system can eliminate the need for additional workers, saving you the hassle of finding the right person.
Depending on the type of system you install, a different range of functions will be available. A common feature is the ability to automatically reorder stock when your inventory gets low.
Manage your SKUs
To track your inventory, your automation system will rely on stock keeping units (SKUs).
SKUs are the identification codes used to track items. Every product has an SKU, but some that come in multiple shapes, sizes and colours may have multiple SKU codes.
Products with more than one SKU code can cause confusion when it comes to forecasting demand. For example, you may assume that there is no interest in a particular item, when in fact consumers aren’t ordering the item because their size is never in stock.
To manage items with multiple SKUs, high-quality logistics software is necessary. This will allow you to manage all of your SKUs in one place. From this, you can figure out how each of your products are truly performing on the market.
First and foremost, your SKUs should be easy for your computer systems and your staff to understand. For example, it may be worth arranging words according to their importance, avoiding letters that look like numbers, spaces, accents and symbols.
Invest in high-quality logistics software
It’s time to ditch the spreadsheets and budget software, and invest in a high-quality logistics system.
From speeding up operations to centralising control, the right software can do incredible things for your business. By centralising control of your inventory, you can cut costs by eliminating redundant effort. This is particularly useful for complex logistics operations requiring a detailed inventory plan.
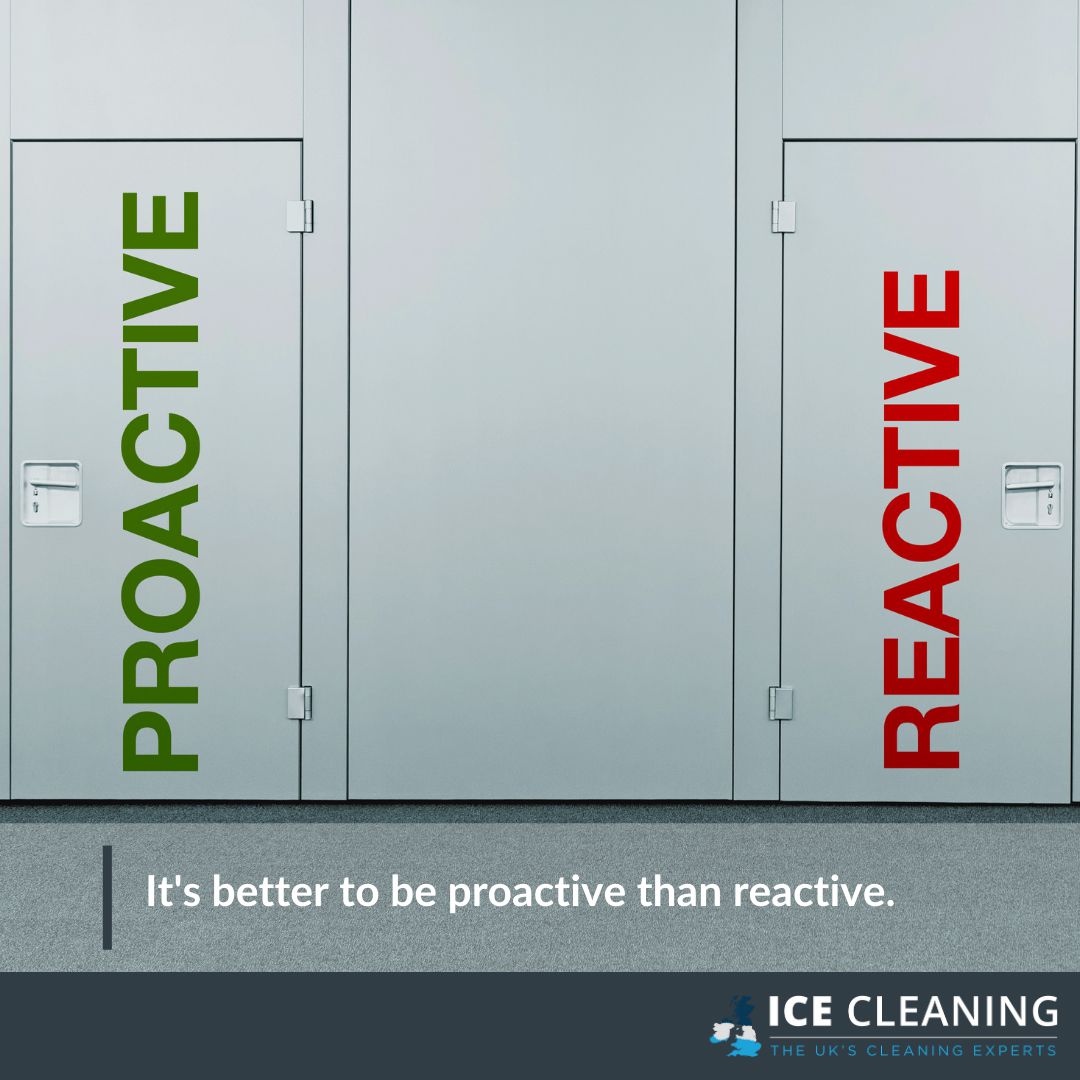
It’s always better to be preventative over reactive.
Through detailed management, you can mitigate the risk of overstocking your warehouse. A high-quality system will be able to provide up-to-date information, allowing your team to make quick decisions.
Dispose of obsolete inventory
Your new management system may reveal that a large portion of your stock is obsolete, in which case it is taking up unnecessary space.
You must resist the hoarder mentality. Remember, if it’s not selling, it’s wasting space in your warehouse. Start by gathering data on the items in your inventory which lack demand and decide on the best option going forward.
It’s important to note that your warehouse staff are not your customers. Whilst employee discounts are a nice perk, if you need to dispose of items promptly, charity is not the most effective solution.
Throwing away obsolete stock is just the beginning. Once you’ve disposed of the items, how are you going to prevent the problem from coming back up?
The key is to adjust your demand forecasts in relation to expected sales. From this, you’ll be able to determine the exact quantities of merchandise required.
Monitor workforce performance
After the level of stock required has been confirmed, turn your focus to your workforce.
Referring to key performance indicators (KPIs), you can assess the productivity of your workers and compare the results against industry benchmarks. Those consistently performing below their objectives will be a cost to your business.
If your staff are not meeting targets, it could be a sign that they are not happy. Employee satisfaction is crucial to drive your operational strategy.
In light of the current pandemic, one reason your staff may be working behind schedule could be that they do not feel comfortable in the workplace. To fix this, it may be worth hiring a professional cleaning company to ensure your warehouse is clean and safe.
Dedicating time to creating a cleaning schedule may feel like a chore in the short-term, but your company will reap the benefits for years to come. It’s a small price to pay for a high reward.
By delegating the cleaning needs to the experts, you can benefit from smoother operations for very little involvement. A clean warehouse will allow your teams to work smarter, faster and happier, resulting in higher profits.
ICE Cleaning
Here at ICE Cleaning, we’re paving the way for the industrial cleaning sector in the UK.
We offer professional, reliable solutions for warehouses and storage facilities. From warehouse cleaning to coronavirus decontamination, we’re a one-stop shop for all your cleaning and hygiene needs.
Using ICE Shield™ technology, we can provide you with the peace of mind that your profits will not fall as the result of illness in the workplace.
To find out more, give us a call today on 0208 066 0360 or email us on enquiries@icecleaning.co.uk.
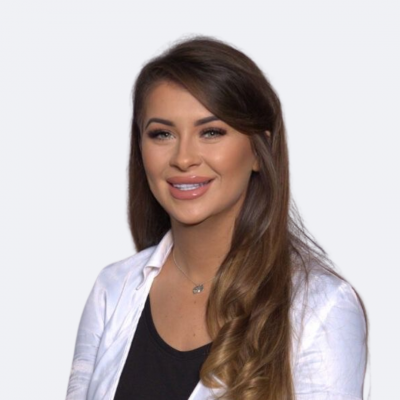
Speak with me today,
I’m here to help
By asking you a few questions either via phone or email I can immediately provide a realistic estimation of the cost.
You’re in good company. We’ve cleaned for the following commercial clients… View all
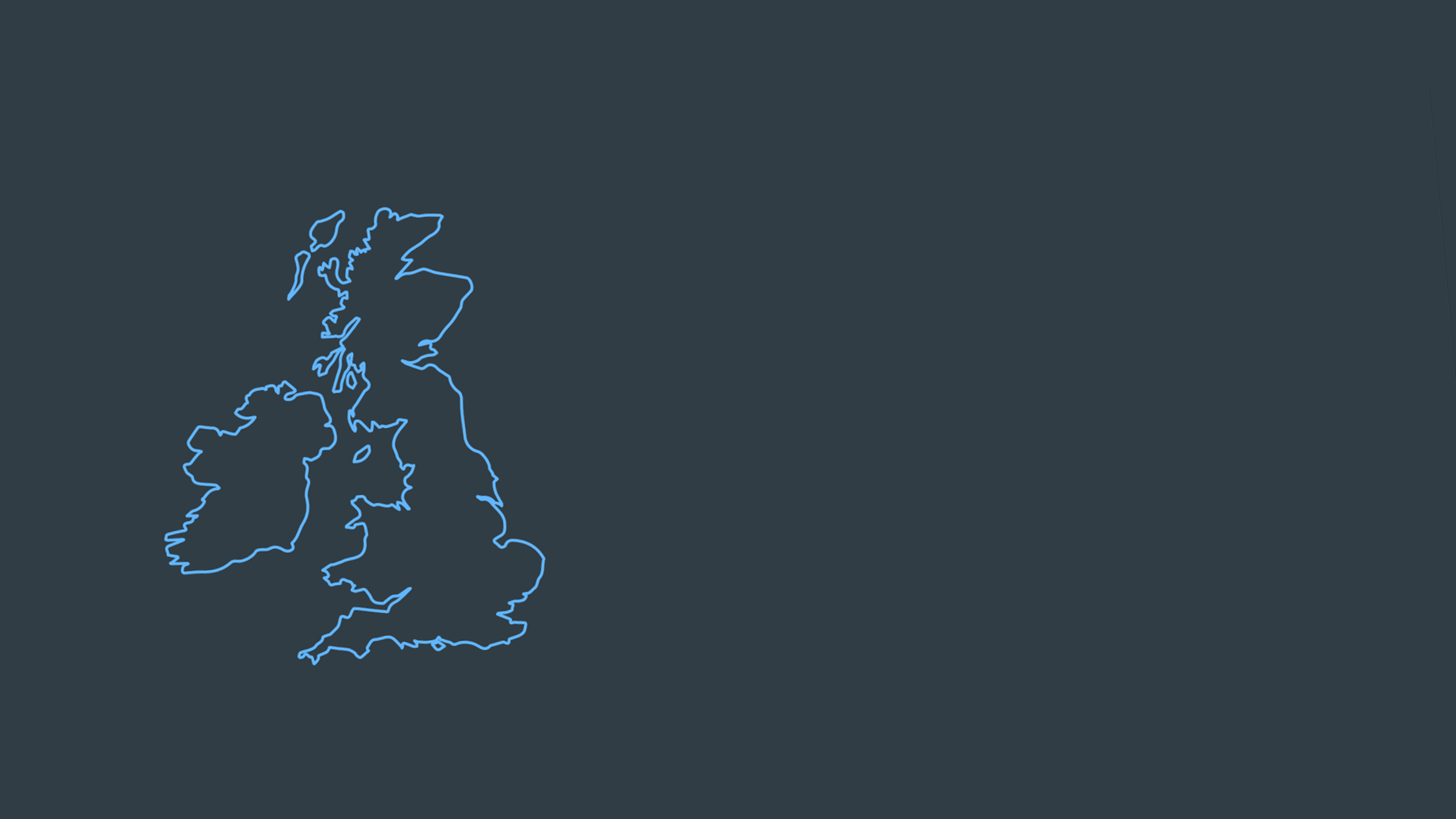
Why choose us?
- Cater to a wide variety of cleaning situations
- Nationwide coverage, available 24/7
- Cater to commercial and domestic clients
- Free survey provided prior to quotation
- Emergency response team
- Offer a bespoke service designed to suit all your needs
- All technicians hold professional health and safety qualifications, including BICSc, IOSH, Dewpoint Professional & Safe Contractor
We’re fully accredited
We place best practise, professional expertise and health and safety at the core of our business. We’re fully compliant with all legal obligations. You can view a list of our accreditations below, or visit our Health & Safety page for more information.
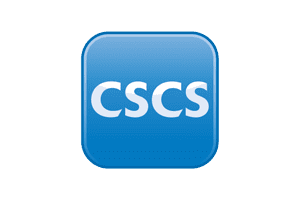
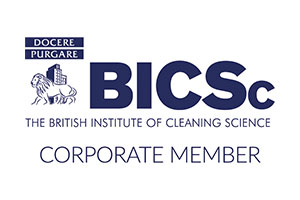
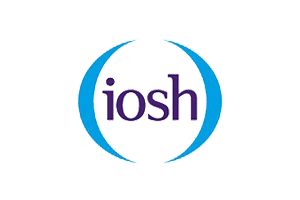
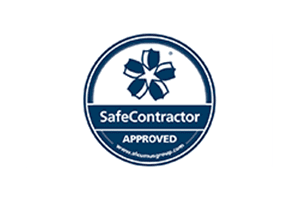
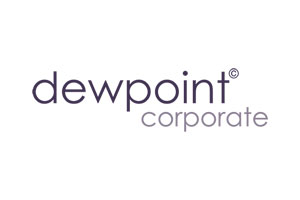
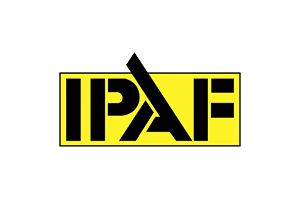
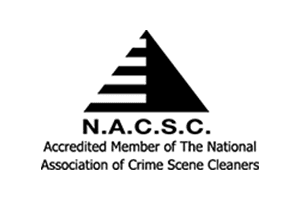